In today's fast-paced technological era, physibots have become integral tools in various industries. However, the term "malfunctioning physibot" is increasingly becoming a concern among users and operators alike. When these advanced machines fail to perform as expected, it can lead to significant disruptions and challenges. Understanding the root causes of these malfunctions is crucial for maintaining operational efficiency.
Physibots, which are physical robots designed to automate tasks, are deployed in industries ranging from manufacturing to healthcare. Their reliability and precision are key factors in ensuring smooth operations. However, when they malfunction, it not only affects productivity but also raises safety concerns. This article delves into the causes, impacts, and solutions related to malfunctioning physibots.
Whether you're an operator, engineer, or simply someone interested in the world of robotics, this comprehensive guide will provide you with the insights you need. From technical glitches to environmental factors, we'll explore all possible reasons behind physibot malfunctions and how to address them effectively.
Read also:Dabigbounce Twitter A Comprehensive Guide To The Viral Sensation
Table of Contents
- What is a Physibot?
- Common Causes of Physibot Malfunctions
- Impact of Malfunctioning Physibots
- How to Diagnose Physibot Malfunctions
- Preventive Measures Against Malfunctions
- Repairing Malfunctioning Physibots
- Industry Standards and Regulations
- Case Studies: Real-Life Examples of Malfunctions
- Future Technologies to Reduce Malfunctions
- Conclusion and Call to Action
What is a Physibot?
A physibot refers to a physical robot designed to perform specific tasks in various environments. These machines are equipped with advanced sensors, actuators, and algorithms to execute complex operations with precision. The term "physibot" encompasses a wide range of robots, from industrial robots in manufacturing plants to collaborative robots (cobots) in healthcare settings.
Physibots play a vital role in enhancing efficiency and reducing human error. However, when they malfunction, it can lead to significant operational challenges. Understanding the nature and purpose of physibots is essential in addressing potential issues that may arise.
Variations of Physibots
Physibots come in various forms, each designed for specific applications. Below are some common types:
- Industrial Robots: Used in manufacturing for tasks like welding and assembly.
- Service Robots: Deployed in service industries for tasks such as cleaning and delivery.
- Medical Robots: Utilized in healthcare for surgeries and patient care.
- Agricultural Robots: Employed in farming for planting, harvesting, and monitoring crops.
Common Causes of Physibot Malfunctions
Malfunctioning physibots can result from a variety of factors, both internal and external. Identifying these causes is the first step in preventing and resolving issues. Below are some of the most common causes:
1. Software Glitches
Software issues are one of the leading causes of physibot malfunctions. These can include bugs, corrupted files, or outdated software versions. Regular updates and thorough testing are essential in mitigating these risks.
2. Hardware Failures
Hardware components such as motors, sensors, and actuators can wear out or fail over time. Regular maintenance and inspections are crucial in identifying potential hardware issues before they lead to malfunctions.
Read also:Zenless Zone Zero Shower The Revolutionary Approach To Mindful Hygiene
3. Environmental Factors
External factors such as temperature fluctuations, humidity, and dust can affect the performance of physibots. Ensuring optimal operating conditions is essential for maintaining their functionality.
Impact of Malfunctioning Physibots
The impact of malfunctioning physibots can be significant, affecting both operational efficiency and safety. Below are some of the key impacts:
Operational Downtime
When a physibot malfunctions, it often leads to operational downtime, resulting in lost productivity and revenue. In industries where time is critical, such as manufacturing, this can have severe consequences.
Safety Concerns
Malfunctioning physibots can pose safety risks, especially in environments where they interact with humans. Ensuring the safety of operators and workers is paramount in addressing these concerns.
How to Diagnose Physibot Malfunctions
Diagnosing the cause of a physibot malfunction requires a systematic approach. Below are some steps to follow:
Step 1: Check Error Codes
Most physibots are equipped with diagnostic systems that generate error codes when a malfunction occurs. These codes can provide valuable insights into the nature of the issue.
Step 2: Review Maintenance Logs
Reviewing maintenance logs can help identify patterns or recurring issues that may have contributed to the malfunction. This information can be used to prevent future occurrences.
Step 3: Conduct a Visual Inspection
A visual inspection of the physibot can reveal physical damage or wear and tear that may not be immediately apparent through error codes or logs.
Preventive Measures Against Malfunctions
Preventing physibot malfunctions requires a proactive approach. Below are some preventive measures:
Regular Maintenance
Scheduling regular maintenance checks is essential in identifying and addressing potential issues before they lead to malfunctions. This includes cleaning, lubrication, and component replacement as needed.
Software Updates
Keeping the software up to date ensures that the physibot is running the latest version with all necessary bug fixes and improvements. Regular updates also help protect against security vulnerabilities.
Training and Education
Providing adequate training and education for operators and maintenance personnel is crucial in ensuring that they are equipped to handle any issues that may arise.
Repairing Malfunctioning Physibots
Repairing a malfunctioning physibot requires a combination of technical expertise and specialized tools. Below are some steps to follow:
Step 1: Isolate the Problem
Identifying the root cause of the malfunction is the first step in the repair process. This may involve troubleshooting software, inspecting hardware components, or consulting with experts.
Step 2: Replace Faulty Components
Once the problem has been identified, faulty components should be replaced with new ones. This may involve sourcing parts from the manufacturer or authorized suppliers.
Step 3: Test the System
After repairs have been made, the physibot should be thoroughly tested to ensure that it is functioning correctly. This may involve running diagnostic tests and simulations to verify performance.
Industry Standards and Regulations
The robotics industry is governed by a set of standards and regulations designed to ensure the safety and reliability of physibots. Below are some of the key standards:
ISO Standards
The International Organization for Standardization (ISO) has established several standards for robotics, including ISO 10218 for industrial robots and ISO 13482 for personal care robots. These standards provide guidelines for design, operation, and maintenance.
Regulatory Compliance
Compliance with local and international regulations is essential for ensuring the safe operation of physibots. This includes adhering to safety regulations and obtaining necessary certifications.
Case Studies: Real-Life Examples of Malfunctions
Examining real-life case studies can provide valuable insights into the causes and solutions of physibot malfunctions. Below are two examples:
Case Study 1: Automotive Manufacturing
In a major automotive manufacturing plant, a physibot used for welding malfunctioned due to a software glitch. The issue was resolved through a software update and thorough testing, resulting in minimal downtime.
Case Study 2: Healthcare
A medical robot used for surgeries experienced a hardware failure due to wear and tear. Regular maintenance checks were implemented to prevent future occurrences, ensuring patient safety.
Future Technologies to Reduce Malfunctions
Advancements in technology are paving the way for more reliable and efficient physibots. Below are some emerging technologies:
Artificial Intelligence
AI-powered diagnostic systems can predict potential malfunctions before they occur, allowing for proactive maintenance and repairs.
IoT Integration
Integrating physibots with the Internet of Things (IoT) enables real-time monitoring and data analysis, providing valuable insights into their performance and condition.
Conclusion and Call to Action
In conclusion, understanding the causes, impacts, and solutions related to malfunctioning physibots is essential for maintaining operational efficiency and safety. By implementing preventive measures, adhering to industry standards, and leveraging emerging technologies, we can reduce the likelihood of malfunctions and ensure the smooth operation of physibots.
We encourage readers to share their experiences and insights in the comments section below. Additionally, feel free to explore other articles on our site for more information on robotics and related topics. Together, we can continue to advance the field of robotics and improve the reliability of physibots.
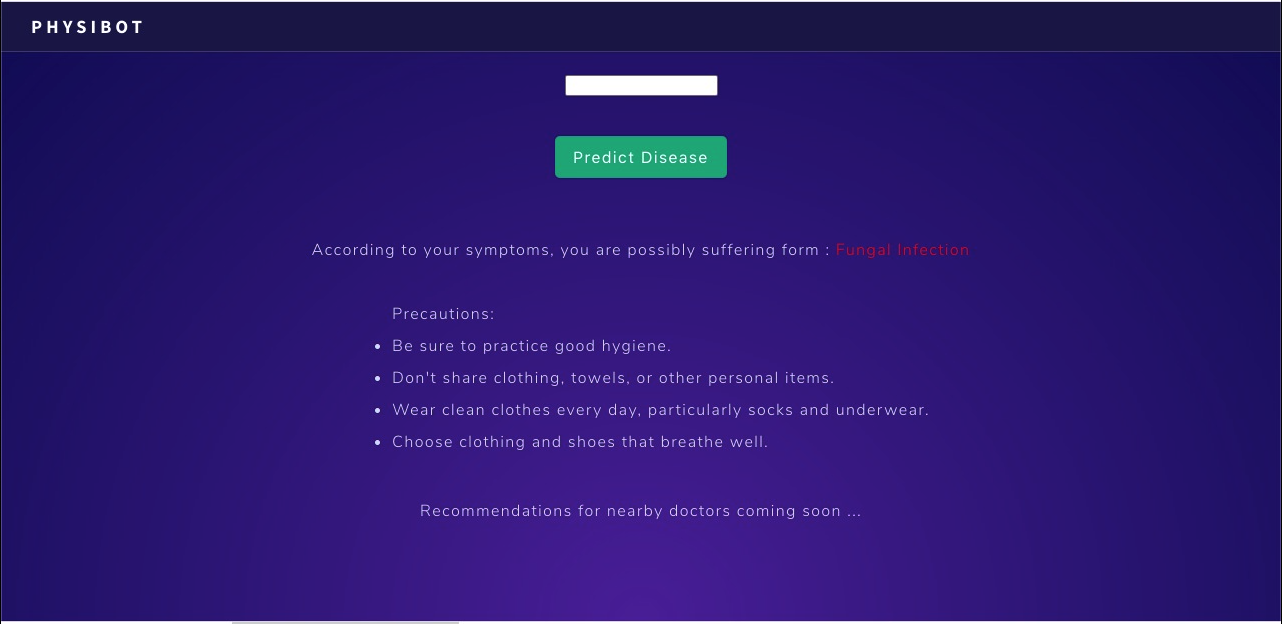
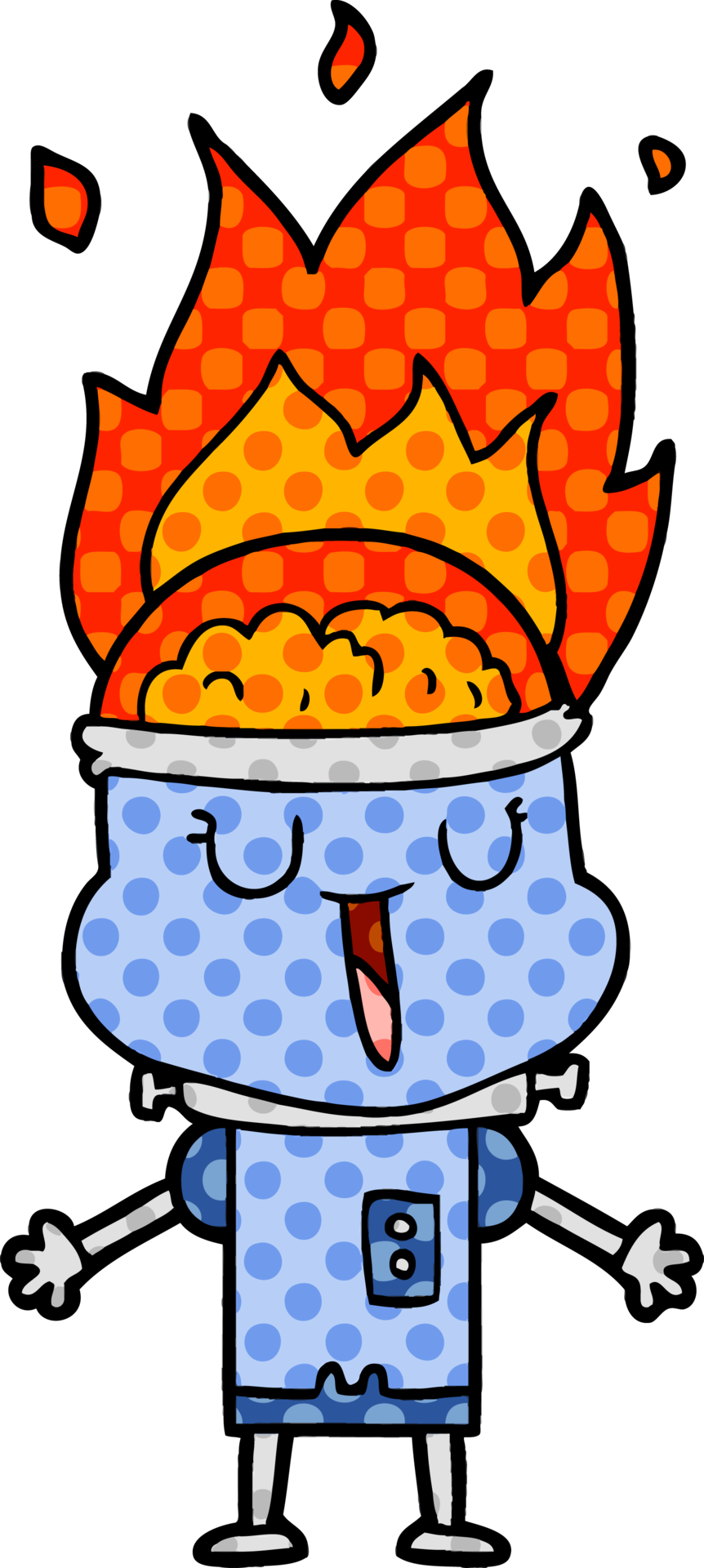
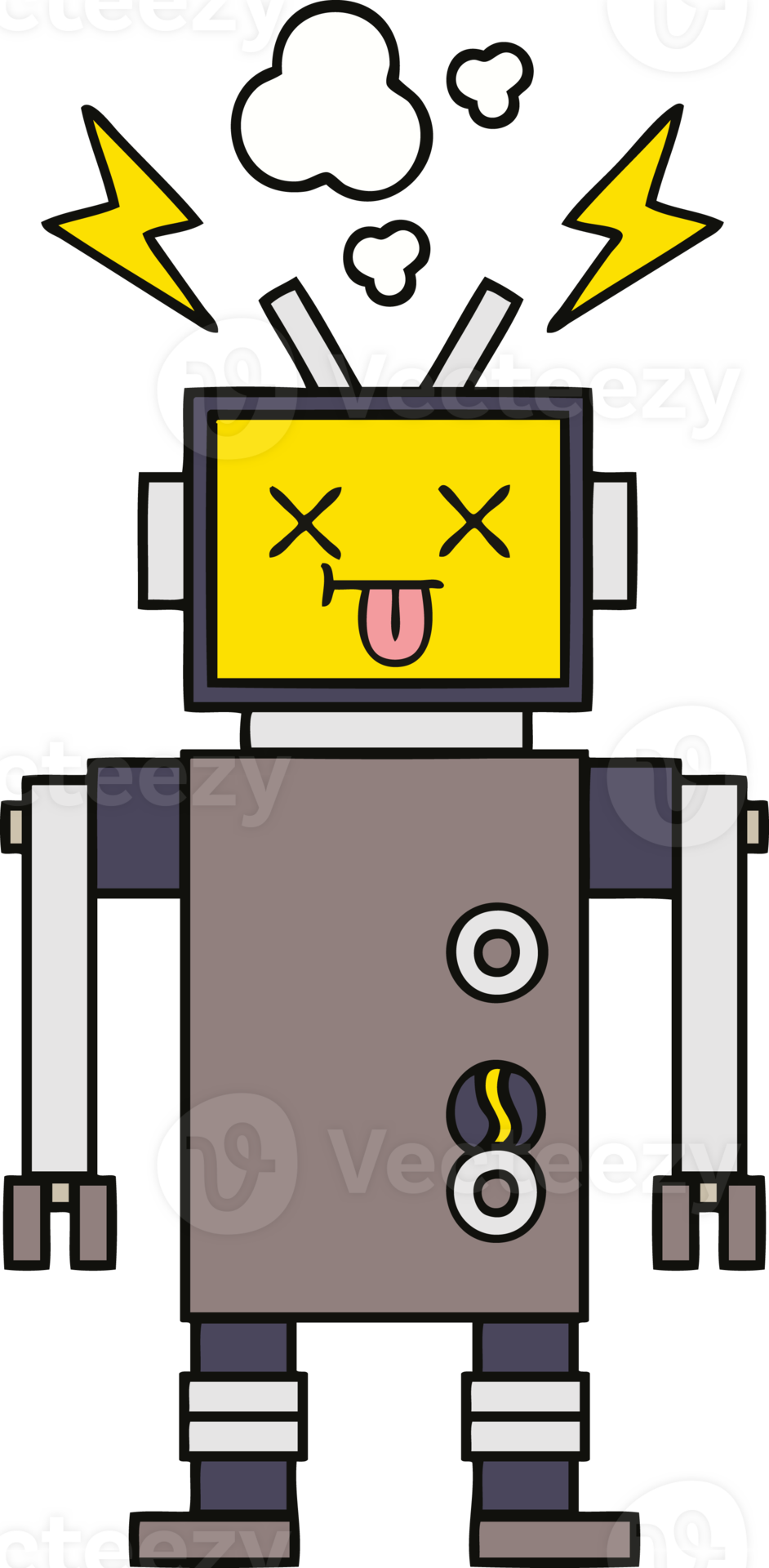